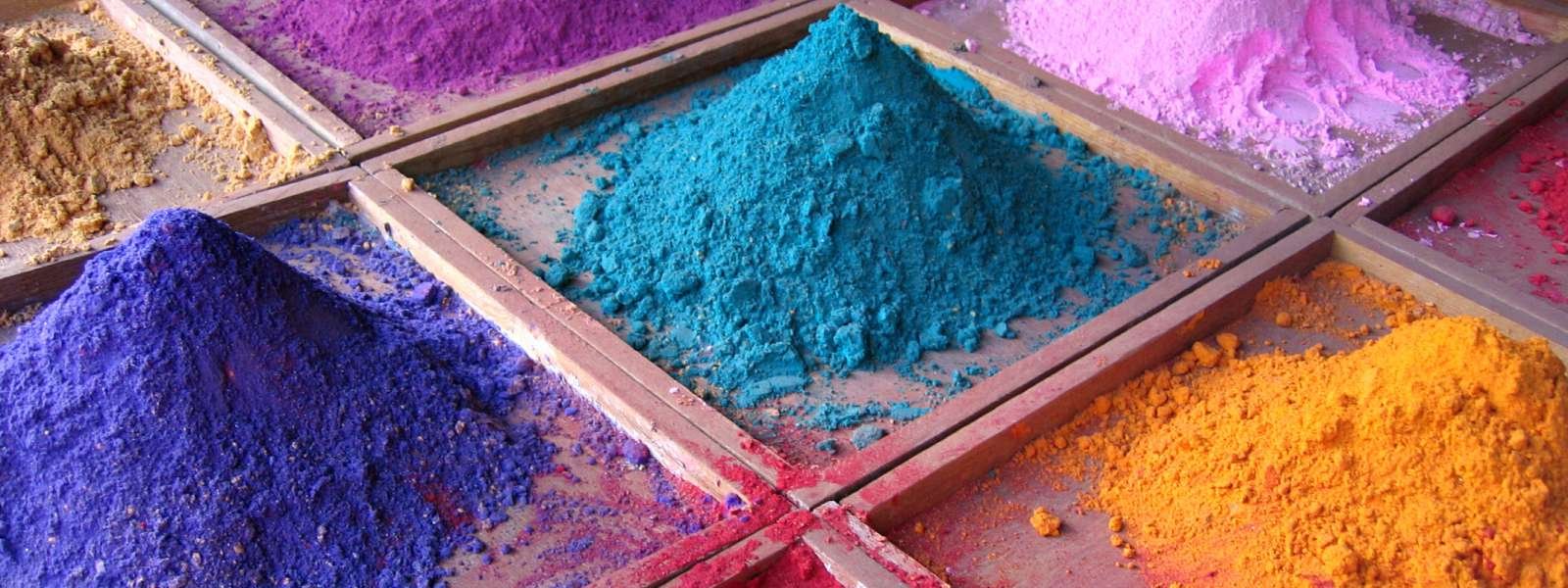
Indigo dyeing and what is being dyed?
NATURAL DYES AND THE ORGANIC INDIGO VAT
Indigo dyeing is a vat dyeing process. To get the dye onto the yarn or the fabric, it is dissolved in water with the help of a reducing agent. Once the yarn or fabric is taken out of the dyeing vat and gets in contact with the atmospheric oxygen, the oxidation process binds the color molecules to the fibers of the yarn during which color of yarn or fabric changes from green / turquoise to blue like magic!
Fabric that is carefully prepared and folded
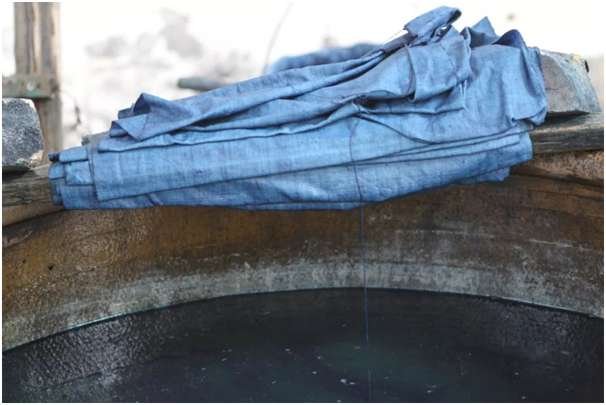
Indigo dyeing, what is being dyed?
Before dyeing, artisans fold the fabric into a workable size and pile it up on a timber board against the edge of the dye vat.
Instead of hurrying up to dye the fabric, they walk to the fabric, bend down then pick up two corners of fabric with two hands. These all seems too natural and obscure, however after a few more views, a sense of ceremony arises in the scene. A dyeing ceremony. If an artisan respects and takes care of what he/she dyes, he/she would make good preparation in every details to make sure items dyed are of good quality, of good value. What’s to be dyed carries love and care of the artisans, right from the beginning it makes a difference in the result.
Layer by layer

The fabric is gently introduced into dye vat layer by layer, with same gesture and same slow speed.
No rush, no haste, give them plenty of time to get into a new environment and accustom to it. This not only eliminates chances of air bubbles being taken into the dye vat as air bubble affects quality of dyeing but also helps each part of fabric take dye evenly and consistently. Fabric needs time to settle into a new place. One dye vat side at the same time, this slow, repetitive and seemingly boring movement gives dye vat time too to accept and embrace fabric that just entered.
There are some subtle but crucial changes happening in dye vat. For example, the more fabric enters into dye vat, the more likely to have fabric touch dye mud on the bottom of dye vat which needs to be avoided otherwise color on fabric would be uneven. So taking notice, taking care of these changes then taking corresponding actions to work with these changes are critical to color on fabric.
The artisan would consider what speed he/she should apply to ensure fabric is off bottom of dye vat. Hence, in the video you see once the last layer of fabric is into dye, he rapidly guides fabric to opposite direction to which it was introduced into vat. This way he “grabs” the first layer that is about to touch bottom of vat. Thoughts and care artisans take at dyeing process bring life and soul to what they dye, to ensure a beautiful indigo fabric is created in the end.
Flowing opportunities
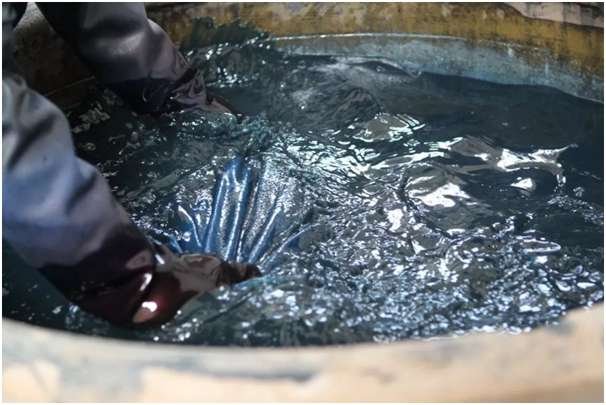
Artisans allow dyes flow freely in the vat while look for opportunities to keep fabric well under controlled at the same time remain relaxed to achieve quality indigo dyed fabric.
What opportunity? And how? One opportunity is like, hands “flow” as dyes do at same speed and same trajectory. This way hands are static in relation to fabric. Feel the fabric and caress fabric to let all area and corner of fabric open up at its comfort so that dye can be taken on evenly. Another opportunity is using anitia and friction of flowing dye liquid to grab fabric when it’s about to touch bottom of vat. These opportunities pop out during dyeing await you to take or create. Should artisans are not focused or work with fabric and vat, they would just flow by before they even realize.
Light colored dye vat
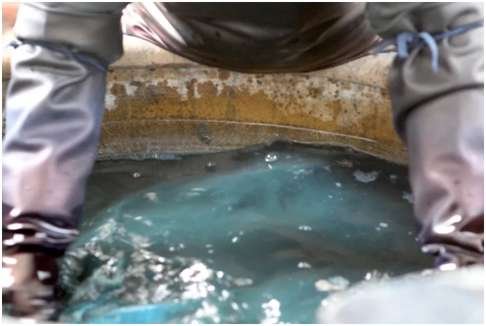
Dye vat should be light colored instead of dark. It takes longer time to dye but it gives evenness of color on fabric.
This will allow enough time for dye to penetrate and settle down on fabric fiber. Though longer time is taken for dyeing but this is not our concern. What we concern about is quality of dyed fabric.
Artisan’s back

Artisans use their waist as a pivot point lean against dye vat so they can bend a bit and lean toward vat a bit for best position to adjust hand location in relation to fabric.
It takes approximately 20 min to dye a piece fabric once. Once dyeing gets started, it cannot be paused or stopped until finished. Therefore artisans have to keep same leaning posture for the entire process to ensure each area of fabric picks up dye evenly. Hence persistence is important for dyeing a quality piece of fabric. Our artisans commit to quality products. This commitment is for ourselves, for fabrics we dye and especially for those who use fabrics dyed by us.

https://affordable-kind-craft.com.au/product/natural-indigo-hand-dyed-cotton-fabric/
Fabric color after first dip is light blue. It’s then dried in the sun. If deeper color is desired more dips are required. Between dips fabric is dried in the sun. So darker colors take longer time to dye. Our darkest color in the range needs up to 10 days to achieve. It’s a process of labor and nature.
So, Indigo dyeing, what is being dyed? The answer may be found in the text or in the dyeing process you experience. Or there might be no answer yet. What’s more important, have you started pondering on this question?
Courtesy: the article is edited based on materials provided by ShilanIndigo .